利用爆炸焊接+熱軋工藝制備鈦-鋼復合板的生產工藝較為成熟,制備的復合板兼具鈦材的高比強度、優良的耐蝕性及鋼材的高強度、良好的塑性和易焊性,成本低,生產效率高,產品生命周期長,已成為現代工業不可缺少的結構材料,廣泛應用于石油、化工、船舶和電力等行業[1-3]。
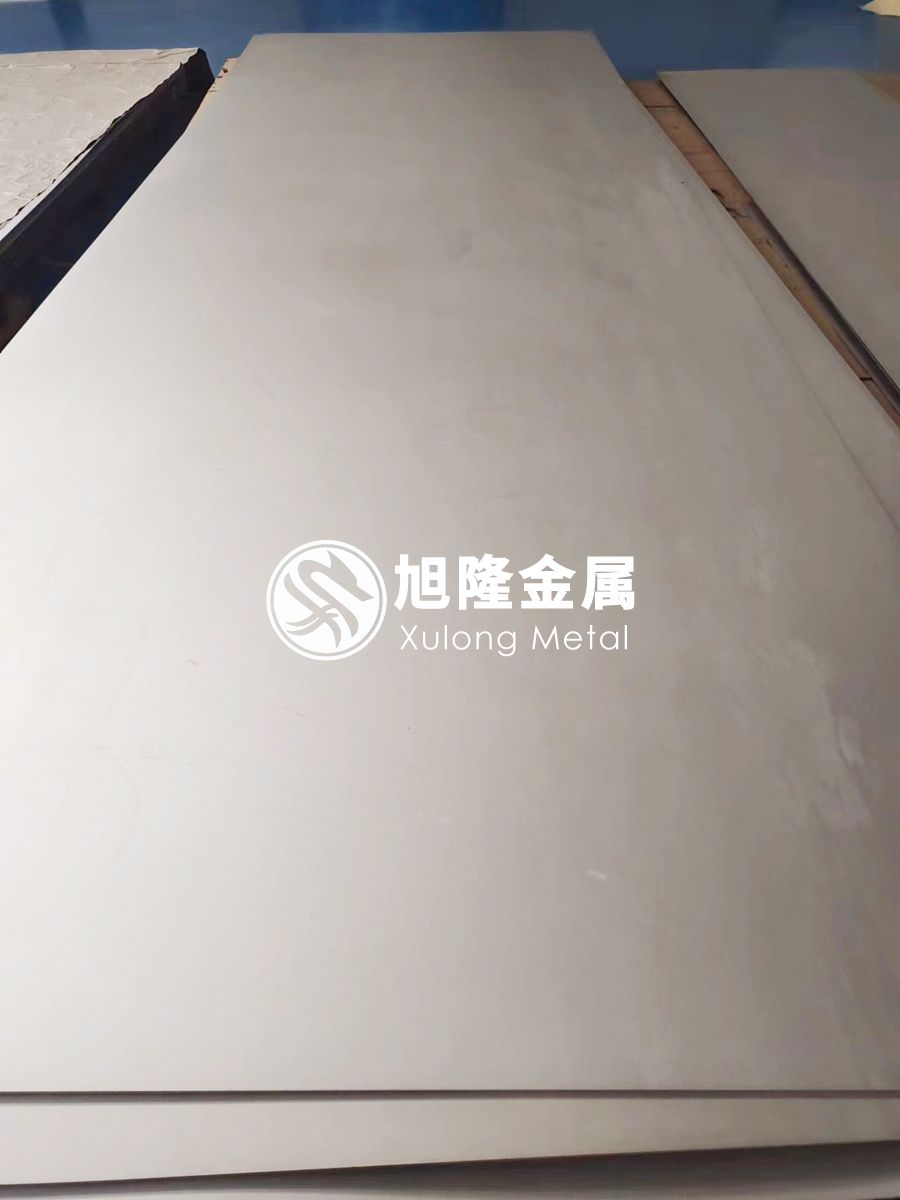
鈦-鋼爆炸焊接具有一定難度和特殊性,為獲得大面積鈦-鋼復合板,通常采用爆炸焊接+熱軋工藝。鈦-鋼復合板的結合質量是保證工程結構能夠安全服役的關鍵,原料和生產過程控制不當,將顯著降低鈦-鋼復合板的結合強度。本研究以爆炸焊接+熱軋工藝制備的鈦-鋼復合板為研究對象,分析由于鈦板表面質量造成的復合界面缺陷,進而優化生產工藝,保證鈦-鋼復合板的性能滿足相關要求。
1、試驗材料與方法
采用爆炸焊接+熱軋工藝生產鈦-鋼復合板,復層和基體分別為6mm TA1鈦板和30mm Q235B鋼板,其性能見表1。采用線切割截取試樣,測試鈦-鋼復合板性能:拉伸和剪切試驗分別按照GB/T 228.1—2010《金屬材料拉伸試驗第1部分:室溫拉伸方法》和GB/T 6396-2008《復合鋼板力學及工藝性能試驗方法》進行測試;使用OLYMPUSGX71金相顯微鏡進行金相分析,采用Hanemann顯微硬度計進行硬度測試,采用氫氟酸(5ml)+硝酸(12ml)+水(83ml)溶液進行鈦組織蝕刻。
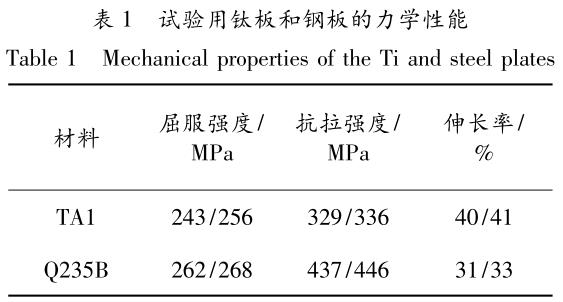
2、結果與討論
2.1復合板力學性能對比
復合板的理論抗拉強度為Rm=(t1.Rm1+t2.Rm2)/(t1+t2) (1)
其中,Rm為復合板強度下限標準值,Rm1和t1是基材強度下限標準值和厚度,Rm2和t2是復材強度下限標準值和厚度。
經超聲波探傷,復合板內部區域結合良好,沒有發現超標缺陷,周邊局部未復合區在20~100mm之間,屬于爆炸焊接過程邊界效應區。
對軋制后的復合板進行550℃×1.5h退火,退火后取樣測試,取樣位置見圖1。表2所示是復合板正常區域和異常區域鈦板的性能,不同區域的強度均高于理論強度;內部正常區域的剪切強度高于196MPa,強度波動較小,說明復合板各區域結合強度較均勻;而邊部有幾組剪切強度不均勻,部分數據低于140MPa,不滿足GB/T8547—2006中其他類復合板要求[4],后續加工時,復合板出現分層的可能性較大。
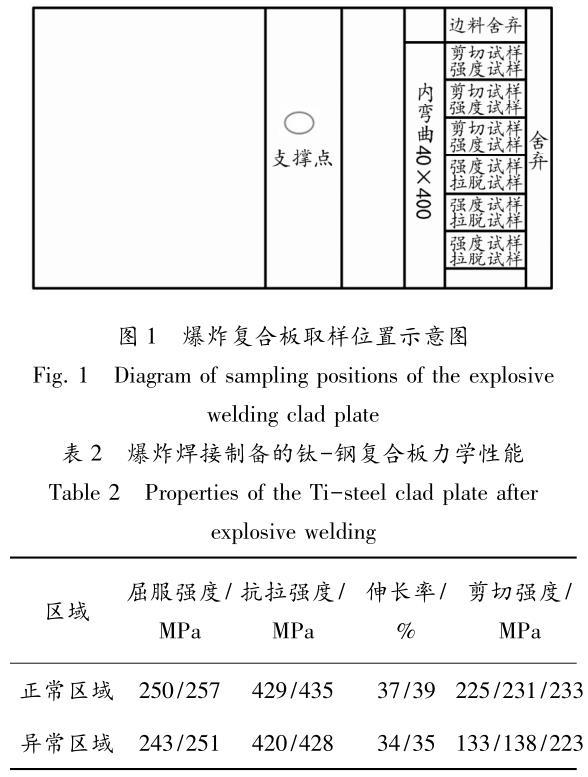
2.2爆炸焊接+熱軋鈦-鋼復合板缺陷
采用爆炸焊接+熱軋工藝制備TA1/Q235B鈦-鋼復合板,鈦板頭尾和邊部區域出現分層、碎邊與皺褶等缺陷,見圖2。對于爆炸焊接鈦-鋼復合板,邊界效應普遍存在,會顯著降低復合板結合面的結合強度和復合率[5],而除了邊界效應造成的缺陷外,分層和碎邊缺陷會影響成品率。
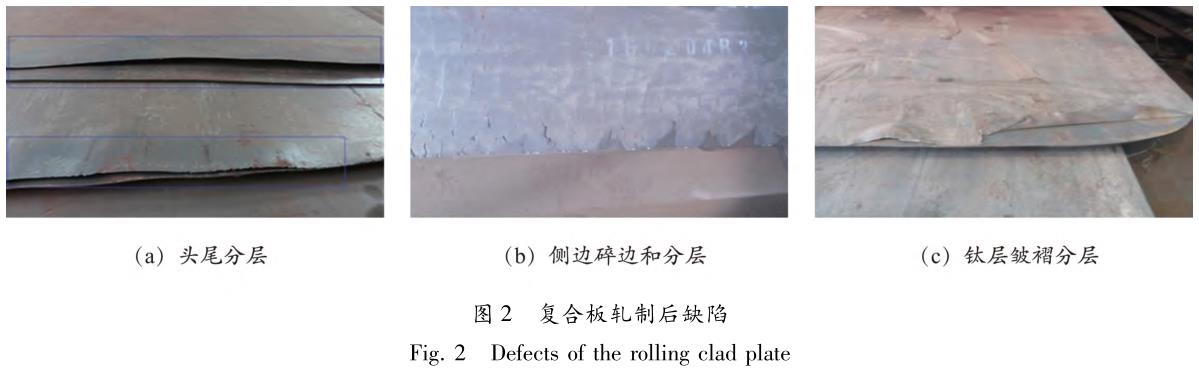
2.3鈦板表面缺陷對復合板性能影響
為了分析復合板產生分層和碎邊等缺陷的原因,重點對鈦板的組織和性能進行分析。
圖3所示是TA1/Q235B復合板爆炸焊接+熱軋后,缺陷附近位置的界面微觀形貌。可以看到,在鈦復合板一側有明顯的裂紋、孔洞、夾雜物和不均勻變形區域等。鈦板中的這些缺陷接近表面區域,可能是由于原材料板坯或半成品缺陷修磨去除不干凈,產生缺陷遺傳,造成鈦板表面夾雜、富氧層和疏松等缺陷,進而在軋制中發生壓入和擴展。
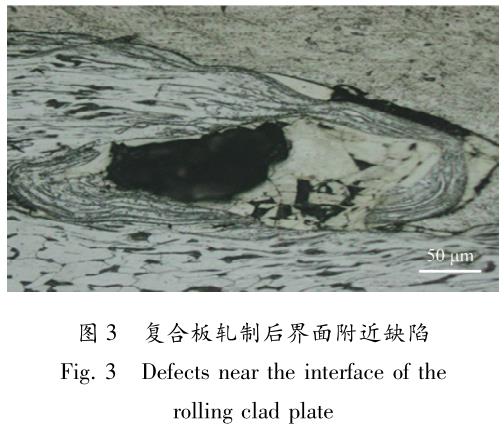
圖4所示是復合板熱軋后鈦板的局部表面缺陷,存在與基體分層的白亮缺陷、與基體連接緊密的較亮缺陷。分層的白亮區域局部最大厚度超過300μm,與基體連接較緊密的較亮區域局部最大厚度超過200μm,主要為氧化層。爆炸焊接復合用鈦板需要進行退火+噴砂+酸洗+拋光,減薄量一般在200μm左右,因此,鈦板表面缺陷過厚時,成品中存在氧化層殘留。
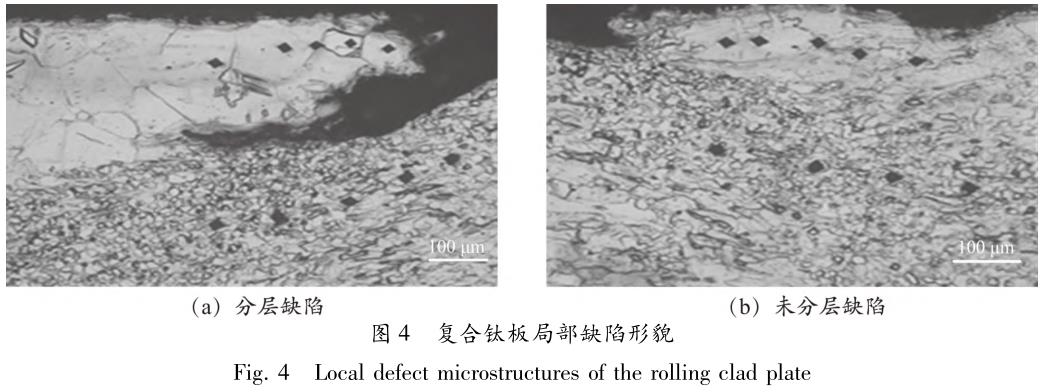
表3所示是圖4中不同區域的硬度測試結果。分層的白亮區硬度最高,未分層的較亮區域硬度也較高,過渡區域硬度次之,正常區域硬度最低。分析確認,表面硬度偏硬區域為氧化層,接近表面區域為富氧層,硬度也高于正常區域的。
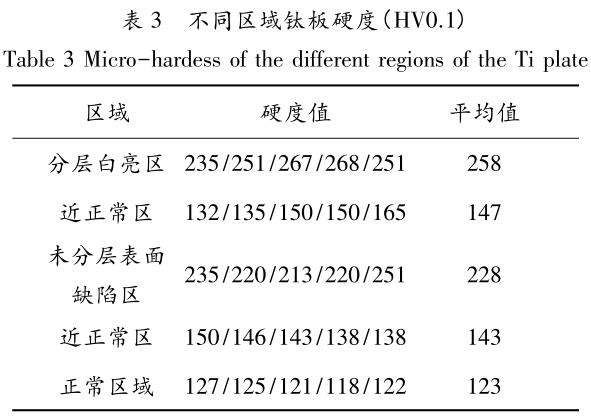
圖5是復合用鈦板表面的局部微裂紋和分層缺陷,在后續的爆炸焊接中,這些缺陷會進一步引起分層和結合不牢等缺陷。
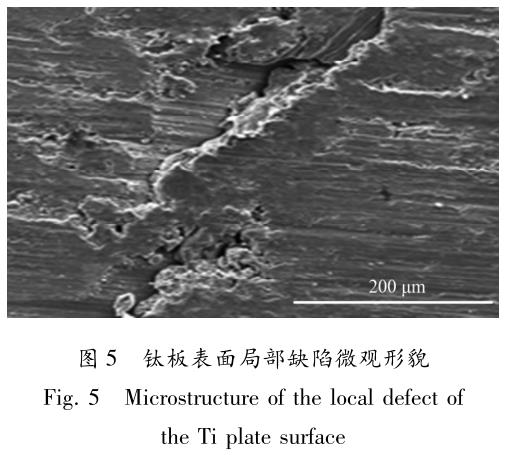
2.4熱壓對鈦板表面的影響
鈦板屈服強度越大,爆炸焊接過程中鈦板應變強化越明顯,塑性變形能力減弱,易形成褶皺性缺陷。通過控制原材料鈦板的屈服強度可使之處于較低的水平,在爆炸焊接時形成穩定、連續的塑性變形[6]。
退火時溫度在600℃以上時,每提高50℃,純鈦的屈服強度會下降10MPa左右。鑒于此,爆炸焊接前,鈦板應在厚鋼板壓制下進行長時間熱壓校形,以獲得良好的性能和板形。但熱壓溫度增高會增加鈦板表面的氧化層厚度,因此,應設計適宜的退火溫度以降低鈦板的屈服強度,避免產生過厚(大于200μm)的氧化層。
圖6所示是650℃和750℃熱壓后鈦板的表面形貌,中間的灰黑色區域是鈦板疊壓貼合造成的結果,邊部氧化劇烈,溫度高時鈦板軟化造成貼合更緊密,氧化和高溫擴散也更顯著。
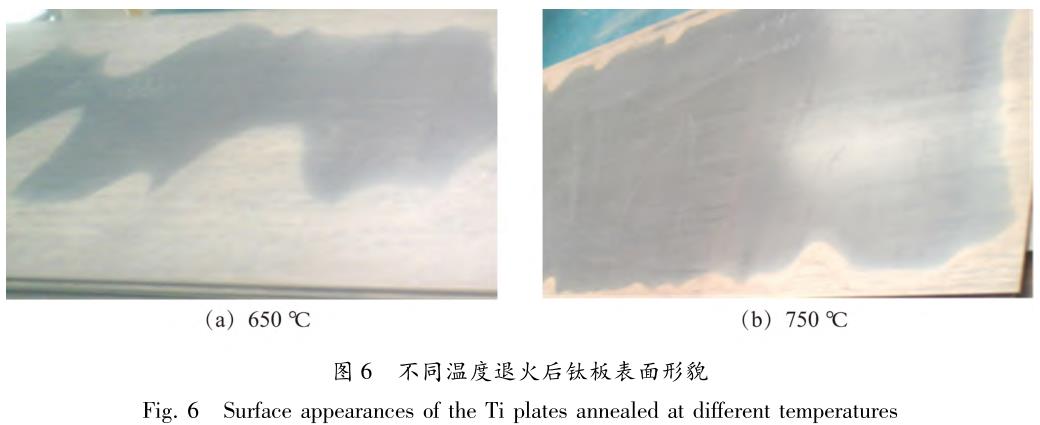
鈦在高溫下與氧、氮等元素劇烈反應,表面形成較厚的吸氣層,硬度升高、塑性降低。圖7是鈦板邊部區域在650℃和750℃熱壓后表面情況,檢測吸氣層厚度分別為50~100μm和80~150μm。鈦板熱壓后邊部區域比中間區域的氧化更明顯,存在不均勻現象,溫度越高氧化層越致密、越厚,需反復多次噴砂酸洗清除氧化層,可能造成板形不良及加工硬化,不利于爆炸焊接。
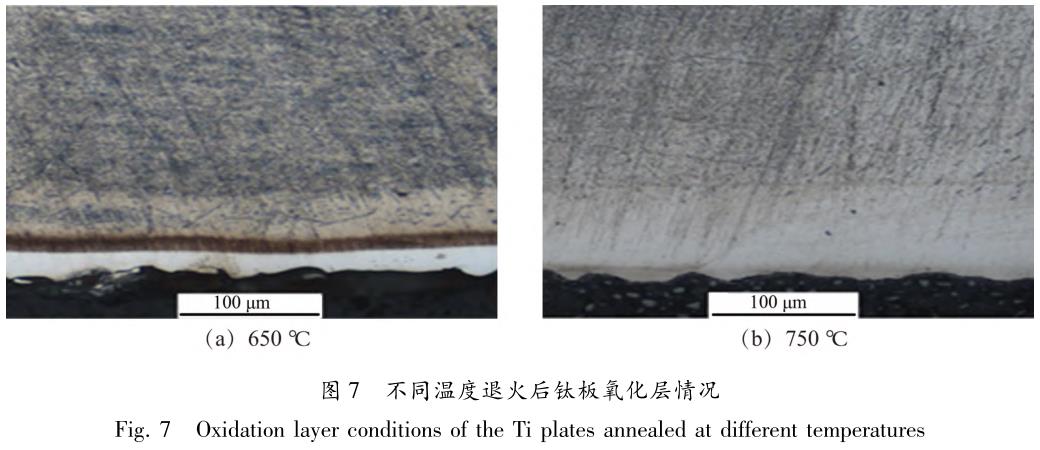
2.5分析與討論
爆炸焊接用鈦板熱壓后表面氧化層可以通過噴砂、酸洗等工序正常去除,但由于原料、熔煉和鈦材軋制加工中一些不可避免的因素,鈦材表面的夾雜、富氧層和疏松等缺陷在軋制中發生較深的壓入和擴展,造成鈦板局部殘留氧化層等缺陷。熱壓鈦板溫度越高,氧化層越致密、越厚,反復多次噴砂、酸洗可能造成板形不良及加工硬化,不利于爆炸焊接。
3、結論
(1)利用爆炸焊接+熱軋工藝制備的TA1/Q235B復合板,出現了碎邊、分層和皺褶分層等缺陷,這與爆炸焊接后復合板邊部局部區域剪切強度低于140MPa、結合不牢固有關。
(2)鈦-鋼復合板軋制后鈦側出現的碎邊、分層和皺褶等缺陷,與鈦板的板形不良和表面的氧化吸氣層厚度較大關系密切。為消除氧化層殘留,需要選用優質鈦錠,板坯和半成品表面缺陷修磨要徹底;選用適宜的熱壓溫度,爆炸焊接前對鈦板進行拋光,去除表面氧化吸氣層,以減少復合時的結合不良問題。
參考文獻:
[1]宋磊,鄒見賓,李松元,等.鈦/鋼爆炸復合板邊界效應的產生與預防[J].有色金屬工程,2015,5(2):1-3.
[2]王小華.電廠煙囪用鈦-鋼復合板鈦復材焊接缺陷產生原因及預防措施[J].材料開發與應用,2012,27(4):102-105.
[3]辛寶,岳宗洪,鄧光平,等.鈦-鋼復合板熱軋工藝研究[J].材料開發與應用,2016,31(6):75-79.
[4]國家質量監督檢驗檢疫總局,中國國家標準化管理委員會.鈦-鋼復合板:GB/T8547—2006[S].北京:中國標準出版社,2006.
[5]王飛,劉廣初,王連來.減小爆炸焊接邊界效應影響研究[J].工程爆破,2005,11(2):6-9.
[6]辛寶,劉金濤,崔衛超,等.鈦的屈服強度對大面積鈦-鋼復合板結合性能的影響[J].材料開發與應用,2015,30(6):10-14.
相關鏈接